오늘날 대부분의 인서트는 초경합금으로 만들어지며 그 주성분은 텅스텐 카바이드(WC)와 코발트(Co)입니다. WC는 블레이드의 단단한 입자이고 Co는 블레이드를 형성하는 바인더 역할을 합니다.
초경합금의 특성을 변경하는 간단한 방법은 사용된 WC 입자의 입자 크기를 변경하는 것입니다. 더 큰 입자 크기(3-5μm)를 가진 WC 입자로 준비된 초경합금 재료는 경도가 낮고 마모가 더 쉽습니다. 더 작은 입자 크기(<1μm)의 WC 입자를 사용하면 더 높은 경도와 더 나은 내마모성을 생성할 수 있습니다. 그러나 취성 카바이드 재료도 더 큽니다. 매우 단단한 금속을 가공할 때 세립 초경 인서트가 잘 작동할 수 있습니다. 반면에 거친 입자의 초경 인서트는 단속 절삭이나 더 높은 인서트 인성이 필요한 기타 작업에서 더 나은 성능을 보입니다.
초경합금 인서트의 특성을 제어하는 또 다른 방법은 WC 대 Co의 함량 비율을 변경하는 것입니다. WC에 비해 Co는 경도가 훨씬 낮지만 인성이 더 우수하므로 Co 함량을 줄이면 블레이드가 더 단단해집니다. 물론 이것은 다시 전체 균형에 대한 문제를 제기합니다. 더 단단한 인서트가 더 나은 내마모성을 갖지만 또한 더 취약합니다. 특정 가공 유형에 따라 적절한 WC 입자 크기와 Co 함량 비율을 선택하려면 관련 과학적 지식과 풍부한 가공 경험이 필요합니다.
경사 재료 기술을 적용하여 블레이드 강도와 인성 사이의 균형을 어느 정도 피할 수 있습니다. 주요 글로벌 공구 제조업체에서 일반적으로 사용하는 이 기술에는 내부 층보다 인서트의 외부 층에 더 높은 Co 함량 비율을 사용하는 것이 포함됩니다. 보다 구체적으로, 블레이드가 파손되지 않고 특정 충격을 견딜 수 있도록 블레이드 외층(두께 15-25μm)의 Co 함량을 증가시켜 유사한 "완충 구역" 효과를 제공하는 것입니다. 이를 통해 인서트 본체는 더 강한 초경합금 조성으로만 달성할 수 있는 다양한 우수한 특성을 얻을 수 있습니다.
원료의 입자 크기, 조성 등과 같은 기술적 매개변수가 결정되면 절삭 인서트의 실제 제조 공정을 시작할 수 있습니다. 먼저 텅스텐 분말, 탄소 분말, 코발트 분말을 비율에 따라 세탁기 크기 정도의 분쇄기에 넣고, 분말을 원하는 입자 크기로 분쇄하고 각종 재료를 고르게 섞는다. 알코올과 물은 밀링 과정에서 첨가되어 두꺼운 검은색 슬러리를 생성합니다. 그런 다음 이 슬러리를 사이클론 건조기에 넣고 액체를 증발시키고 분말 덩어리를 만들어 저장합니다.
다음 준비 과정에서 블레이드의 프로토타입을 얻을 수 있습니다. 먼저, 제조된 분말에 가소제 역할을 하는 폴리에틸렌글리콜(PEG)을 반죽과 같이 일시적으로 결합시키는 역할을 합니다. 그런 다음 재료는 다이에서 블레이드 모양으로 눌러집니다. 다양한 블레이드 프레스 방법에 따라 단일 축 프레스를 사용하여 프레스하거나 다축 프레스를 사용하여 다양한 각도에서 블레이드 모양을 누를 수 있습니다.
프레스 성형된 빌렛을 얻은 후 대형 소결로에 넣고 고온에서 소결합니다. 소결 과정에서 PEG는 빌렛 혼합물에서 녹아서 반제품 카바이드 인서트를 남깁니다. PEG가 융합된 후, 블레이드는 최종 크기로 축소되었습니다. 이 공정 단계는 재료의 조성과 비율에 따라 블레이드의 수축량이 달라지고, 완제품의 치수 공차가 수 마이크론 이내로 제어되어야 하기 때문에 정확한 수학적 계산이 필요합니다.
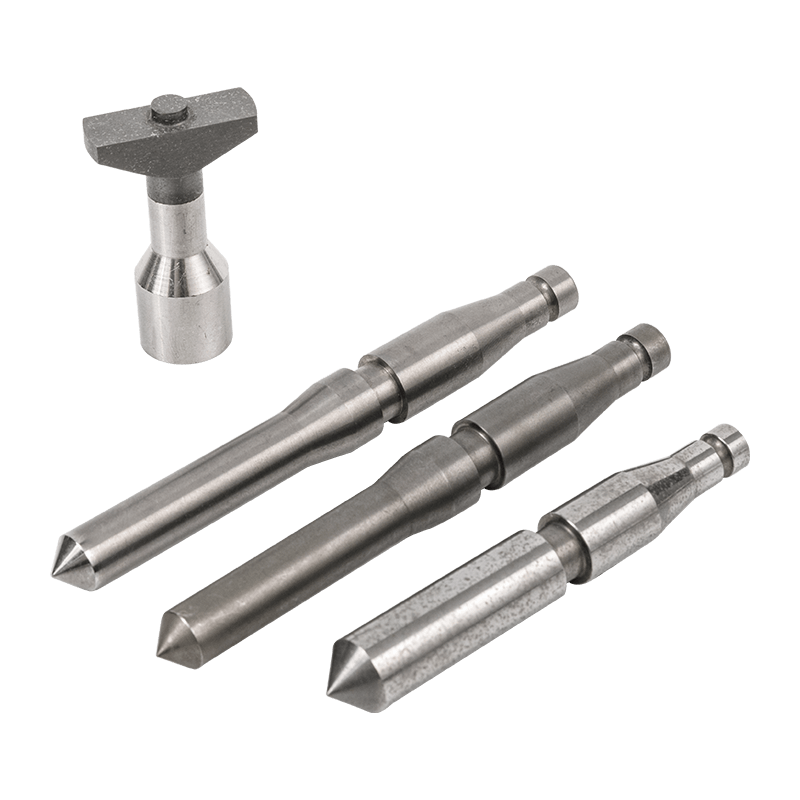